6th Form Business & Economics trip to the MINI Plant, Oxford
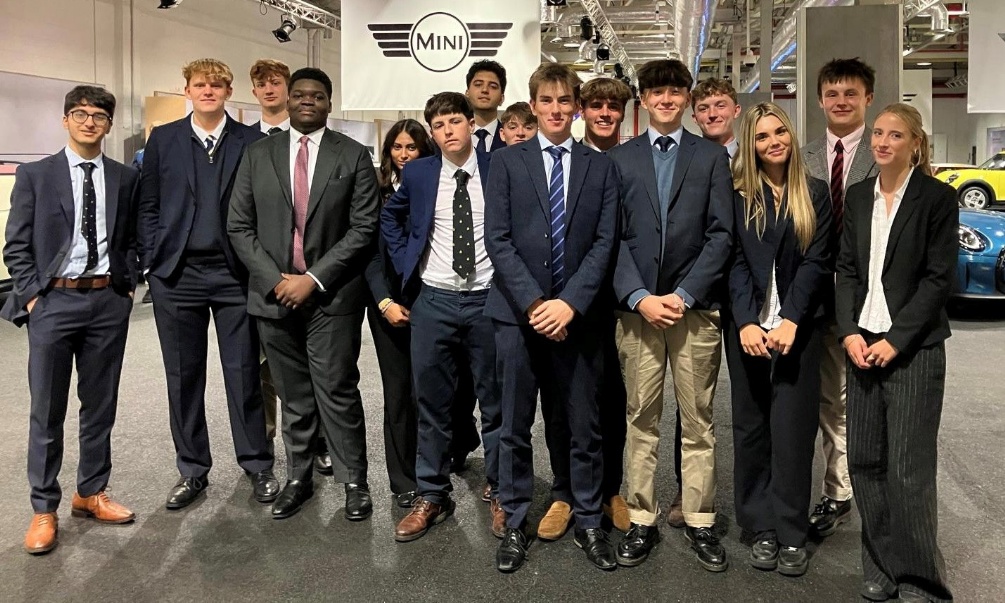
This week, L6th Form 6th Form Business & Economics students visited the MINI assembly plant at Cowley, Oxford. This plant, in one guise or another, has been producing motor cars since 1913.
Many readers of this article will remember with a sense of nostalgia when Cowley was synonymous with Morris Garages and, later on, with British Leyland. However, by the 1970s and with the increasing strength of trade union power in negotiations added to the militancy of their shop stewards and union leaders, Britain lost its place as Europe’s biggest producer of motor cars as the decade became notable for strikes, failed management buyouts by workers (Triumph 1976), and slow to nil productivity growth.
By the mid-1980s, as the UK manufacturing sector failed to keep up with the investment in capital that similar economies had made and continued to make, effectively pricing ourselves out of the market, many of the grand old marques of yesteryear were either sold into foreign ownership or had been forced into receivership before being closed for good. However, this trend was about to be reversed by Honda in Swindon and then Nissan in Sunderland opening state-of-the-art production and assembly lines that introduced new business models and production techniques, all supported by the most sophisticated capital to harness and drive productivity growth. Exploiting the UK’s position within the then Common Market, by the mid-1990s, the UK. had surpassed France to become the second biggest exporter of motor cars behind BMW, something that few would have thought possible only a decade earlier.
In 1996, BMW, as part of its acquisition of the Rover group, acquired the rights to design, produce, distribute and sell the Mini and, after much planning, the first new generation Mini rolled off the Cowley production line in 2001. Since then, there have been seven upgrades or editions to this original. Last year's 295,474 Minis, including the electric version, were sold with over 4.4 million produced at Cowley since its inception.
Today’s plant is spread out over 150 acres compared to the original 700 acres that were being used in the 1970s. Employment on the assembly line has fallen from a peak of 7,000 towards the end of the 1960s to around half of that figure. However, output per hour has almost doubled from 26 motor cars to 48 vehicles per hour on average with a usual output of 60 Minis per hour. This increase in productivity was no more visible than walking around the fully automated production line where hi-tech robots are now filling the roles with greater speed and efficiency than their human counterparts of the past; heavy lifting and the accurate fitting of these parts has been revolutionised, leaving only items weighing less than eight kilograms to be fitted by workers.
While employment has fallen, there have been jobs created in the maintenance of these robots, programming and software development, and training to use and repair capital. Much was made of the lean management techniques, such as value stream mapping, Kanban, as well as the importance of Kaizen being emphasised to employees working at the plant. Already, Mini is in the process of making critical changes to its production and assembly process to accommodate the shift of its electric motor unit plant from China to Cowley: subtle changes to the chassis and bodyshell have already been made to accommodate the different drive mechanism and a new power plant assembly plant is in the early stages of development.
From an academic and educational perspective, this trip was a valuable opportunity to witness a number of important economic and business concepts, from Schumpeter’s theory of creative destruction, to different management theories and models, to the true impact that trade agreements and trading on WTO rules has for countries and local economies.